Originally published in Urban Ag Products Issue 1
There are many factors to consider before starting a greenhouse vegetable operation. greenhouse grower Richard Billekens discusses some of the most imPortant considerations before getting started.
An increasing number of eld vegetable growers and ornamental plant growers are considering adding greenhouse facilities or using current structures to produce vegetables. Richard Billekens has 28 years of experience in the production of greenhouse vegetables. He has worked as a grower in the United states, Canada and Mexico. He has also worked as consultant in the United states, Canada, Mexico, Russia and Sweden. He is currently head grower, production manager and head of research and development at Hortinvest Mexico sA de CV in Querétaro y alrededores, Mexico. He manages 181⁄2 acres of greenhouse- grown sweet bell peppers. Billekens said there are some major factors that growers need to consider before building any structures for vegetable production.
Choosing a location, market
Having experience in numerous production facilities worldwide, Billekens said he has found a location about 2,000 meters (6,561 feet) above sea level to be the best.
“This provides a tropical climate, but it is not too hot and not too cold,” Billekens said. “In locations like Holland and Sweden, growers don’t have a lot of options in regards to location. ey build there because of the closeness to the market. We built in mexico because we also wanted to be close to our market, which is the United states and Canada. From here to Detroit it’s a shorter driving distance than from Vancouver, British Columbia, to Toronto. It’s only a two to three day drive for us.”
Being at a high elevation in Mexico, Billekens said light levels are not an issue.
“In December our facilities receive between 1,400-1,800 joules of light per day. In Vancouver during the same time, daily light levels are only 200 joules,” he said. “But Vancouver has light levels that are much higher than Holland and other northern European locations.
“In Sweden and Russia during the winter, some of the growers use lights to grow. But in those locations using lights can be very expensive. Installing and running lights nearly doubles the cost of building the greenhouses.”
Although the peppers grown by Billeken’s company compete with product grown in Canada and Europe, he said he has the advantage of being able to produce peppers when Canadian and European growers are replanting their crops. He said growers in Canada and Europe usually replant during November and December. He replants his crop during June and July. Like Canadian and European growers, he is producing peppers for 38-40 weeks.
“Pepper growers in Canada and Europe are replanting their crops in December. ere is no production going on,” Billekens said. “That is the time that I am in full production. I start planting the first week of June and go through Christmas time so that I can get a higher return on my product during November through march. Canadian and European growers are in full production in April and May.”
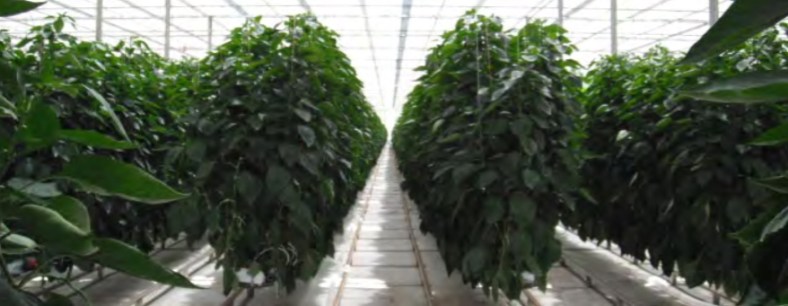
Water source
Billekens said having a reliable and good water source is a critical factor in growing greenhouse vegetables. He uses water from a well which has a sodium level of 2.5-3 millimoles per liter. He said this level is too high for pepper and tomato production. A reverse osmosis system was installed to remove the sodium and bicarbonates.
“It costs about 35 cents per cubic meter to clean the water,” he said. “some elements like sodium and iron are easy to remove from water. Once the water is treated it is very clean.”
Billekens said rain water is the best source of water because it is very clean to begin with. He said rain water can become polluted when it is stored in catch basins. However, cleaning this water prior to use doesn’t usually require as expensive a system or as a large a unit as treating other water sources.
“In Mexico and other desert locations like saudi Arabia there is not much rain. at is why I am using well water,” he said. “surface water is not as clean as well water. surface water can collect all types of contaminants including algae and disease pathogens.
“If a water source has a lot of organic matter in it, the irrigation system can become plugged up very quickly. Sand filters can be used to remove this material.”
[adrotate banner=”23″]
Billekens said growers in Holland also use municipal water supplies. To reduce the demand for water early in the morning, Dutch growers ll holding tanks at night when the demand for water is low. is also enables the growers to pay less for the water they use since they are drawing city water at non-peak periods.
“Some Dutch growers have as many as three options when it comes to water sources, including rain water, city water and well water,” he said. Since city water is the most expensive, most growers try to mix it with rain water at a ratio of half and half.”
The well water Billekens is using has a pH of 7.5. A er the water is treated by reverse osmosis the pH is lowered to 6.5 and it is stored in an outside tank. Acid is then injected to lower the water pH to 6.0. It is then ready to be used for irrigation.
Keeping things simple
Billekens said he has a very simple fertilizer system consisting of a mixing tank with two tanks that contain separate fertilizers. The fertilizers are pumped into the mixing tank where they are diluted with fresh water. A drip irrigation system then delivers the water to the pepper plants, which are being grown in coco fiber bags. Each plant has its own drip line.
“We are using the hanging gutter system to produce the peppers,” Billekens said. “We found that the coco fiber bags are a little cheaper and a little more forgiving in Mexico’s climate, which I consider to be harsh. e hottest time of the year is in April, which is just about the time the crop is finishing. The high temperature is about 38 degrees C (100.4 degrees F) with no humidity, so it is like a desert climate.”
Since the plants are nearly 13 feet (4 meters) tall and covered with a lot of foliage, Billekens has to irrigate between 10 to 20 cycles (5 to 12 liters per square meter per day) to prevent wilting.
“The plants can adjust to the climate in the greenhouse,” he said. “There is a lot of transpiration from the leaves so they are making positive changes to the climate by raising the humidity.”
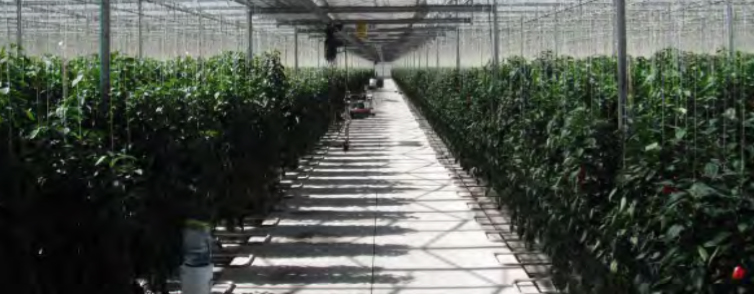
Billekens said a misting system could be installed to raise the humidity, but the water quality has to be very good to ensure there isn’t any clogging of the nozzles. He said a misting system can also be expensive, about $7 per square meter.
Billekens said his company is the only one in Mexico growing peppers in glass covered greenhouses.
“We apply white wash to lower the light intensity from April until September,” he said. “During may we are cleaning the greenhouses and then replanting in June. During that time it’s more comfortable to be in the greenhouses covered with white wash.
“There are other pepper growers in Mexico who have plastic covered greenhouses who also apply white wash to avoid stressing their plants. If the plants grown in plastic greenhouses are healthy, white wash doesn’t usually have to be applied.”
Billekens has installed circulating fans to keep air moving when the greenhouse vents are closed at night. “ e fans aren’t used for cooling at all,” he said. “They are used for air movement. The fans help to prevent powdery mildew and other fungal diseases.”
Don’t skimp on construction
Billekens said it is critical that a grower find a good greenhouse builder when constructing a greenhouse.
“This greenhouse operation is the ninth construction that I have been involved with,” he said. “Regardless of whether you buy an American, Canadian or Dutch greenhouse, ask the manufacturer where the labor is coming from. If you have to hire the builders from Canada or Holland, that could end up being an expensive greenhouse project. The construction costs of the project can increase considerably.”
Billekens said he works with the builder providing 10 to 15 local laborers, including a welder and an electrician, who can handle the simpler construction tasks.
“What I want from the builder are specialists,” he said. “These are specialists who ensure the land is leveled correctly, the greenhouse foundation is laid out properly and the concrete is poured evenly.
“I want someone who specializes in greenhouse construction to come in for five to seven days to make sure the first support post is erected straight. If the first post is put up correctly then the rest of the posts will be straight.”
Billekens said one of the most important parts of building a glass greenhouse is the glazing. He advises growers to spend the money to hire a specialist to install the glazing.
“The glass on the roof has to align correctly,” he said. “If the glass doesn’t align, then there are going to be problems with the roof vents opening and closing and increased chances that the panes will slip and fall out.
“You may spend a little more initially hiring these specialists, but then you know the job is going to be done properly and you won’t have to worry about it later. Also, you want to hire specialists for warranty reasons in case something does go wrong. If you do all of the construction yourself and something does go wrong, then you’re on your own to correct the problems.”
Multi-tasking employees
Billekens said when he started the operation in Mexico he did not have a hard time finding enough people to work in the greenhouse.
“It takes about five people per hectare (2.47 acres) to operate the greenhouses,” he said. “But I hired 10 people since no one had any experience working in a greenhouse. I had to teach them everything about handling the plants and harvesting the peppers.”
Billekens said it was not difficult for the employees to learn how to handle the crop. He has various groups of employees who do the different tasks, including pruning and winding, harvesting the peppers and pest and disease monitoring and management.
“Every employee is very specialized in one particular activity, but they also know something about each of the different tasks performed by the other employees,” he said. “This ensures that if someone is absent, say because of illness, there is another employee who can cover for the missing employee.”
For more: Richard Billekens, Hortinvest mexico sA de CV; rbillekens@yahoo.ca; www.freshmex.com.mx.
David Kuack is a freelance technical writer in Fort worth, Texas; dkuack@gmail.com.