Lettuce being grown as baby greens at Purdue University are harvested 15 days after planting seeds. Seeds are sown close together to minimize loss of photons between plants. Photo courtesy of Cary Mitchell, Purdue Univ.
Researchers with the OptimIA project are working to solve the environmental control issues facing indoor farm growers.
While some might think that the environmental challenges facing indoor farm growers should be relatively minor and easy to overcome in a closed environment, they’d be wrong.
“Some of the challenges and bottlenecks facing indoor farms include insufficient airflow leading to a non-uniform environment, lighting that is wasteful and how light is delivered into the canopy,” said Murat Kacira, director of the Controlled Environment Agriculture Center (CEAC) at the University of Arizona and a member of the OptimIA project research team. “In addition to these challenges, there are those related to the humidity and water management in the aerial environment as well as identifying the best light quality, light intensity and light recipes for indoor farm crops.”
Prior to the start of the OptimIA project in 2019, surveys were conducted of stakeholders in the indoor farm industry, including growers, to determine what are the areas of greatest need for research.
“An indoor farm is a closed box,” Kacira said. “You know what goes in and what comes out, but it demands the resources to control that environment, which include controlling the light, temperature, humidity, carbon dioxide and all other processes to grow the crop to meet production expectations.
“An indoor farm offers tighter control than in a greenhouse environment. There is not the same effect from the outdoor dynamics, for example the light intensity, temperature and water recirculation from the air. Being able to harvest the water from the air is easier in an indoor farm system compared to a greenhouse system. There is more controllability when it comes to an indoor farm compared to a greenhouse, of course with an additional expense for resource use to achieve such control.”
Focused on environmental control
Kacira and his team of graduate students KC Shasteen and Christopher Kaufmann at the University of Arizona are significant contributors on the environmental control aspects of the OptimIA project.
“We are also considering light because light brings the energy to the plants and then the energy has to be released for cooling and for proper transpiration and nutrient deployment from the roots,” Kacira said.
Kacira’s team conducted computer simulations to help improve airflow and to identify co-optimization of environmental variables for energy savings. Building upon computer simulation research outcomes, Kaufmann is conducting experiments in CEAC’s vertical farm facility to evaluate vertical and horizontal airflow system designs to mitigate tipburn on lettuce crops. Shasteen and Kacira worked on modeling with the co-optimization of variables, including light, temperature, relative humidity and carbon dioxide level.
“We have been able to quantify yield outcomes and to determine what the energy use would be for any of those environmental control strategies,” Kacira said. “These models and the outcomes and information that we have generated from this research are used by our OptimIA colleagues on the economics team. They are developing economic models for a variety of scenarios of profitability and economics for indoor farm applications and indoor farm systems.
“We are focused primarily on airflow system design and optimization, humidity management and co-optimization of environmental variables mainly for energy savings. Our collaborations also included Nadia Sabeh at Dr. Greenhouse on the humidity management side of the environmental control aspect.”
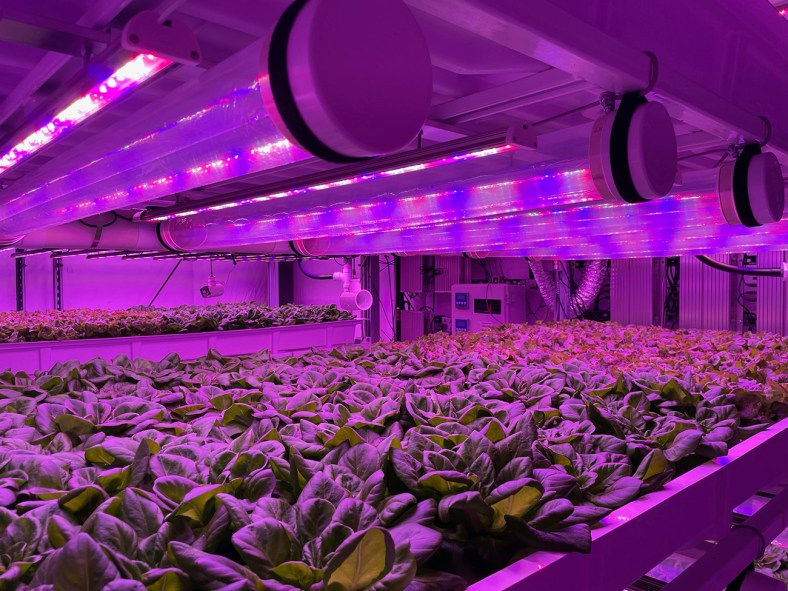
Real-world applications
Some of the research outcomes from the University of Arizona team related to airflow systems designs, concepts and recommendations have been incorporated into actual growing settings in commercial operations.
“We are able to incorporate some of our research results into commercial site trials through our collaborations,” Kacira said. “We have over 20 industry collaborators as part of the OptimIA project. Some of the collaborators showed interest in implementing some of the airflow system designs, environment control, and co-optimization of these variables into their operations. We will also have an opportunity before the OptimIA project ends to implement them directly and evaluate some of the research outcomes in commercial settings.”
Saving on energy costs
Sole-source lighting is the largest energy cost of indoor farms. Indoor farm energy costs account for at least 30 percent of the total operational costs. Other energy costs are related to operating fans, dehumidification and ventilation.
“The focus of the OptimIA research at Purdue University is to identify and try to reduce the energy costs related to growing indoor crops,” said Cary Mitchell, horticulture professor at Purdue University. “If an indoor farm grower is using sole-source lighting that is going to be the biggest energy cost. These indoor farms spend hundreds of thousands of dollars per year on electricity and it’s mostly for lighting.”
Mitchell has long been interested in energy as one of the profit-determining and profit-limiting parameters in indoor farming.
“All of the OptimIA researchers are interested in saving resources for growing leafy greens and culinary herbs indoors,” he said. “That is the common thread among all of us. Purdue researchers are focused on energy savings. “
Avoid wasting light
Mitchell and PhD graduate student Fatemeh Sheibani are working on close-canopy LED lighting. This lighting is similar to intra-canopy lighting that is used on some greenhouse crops including high wire tomatoes and fresh cut roses.
“One of our findings is if the separation distance is reduced between the LED light fixtures and the crop below without dimming the LEDs, the productivity of the plants goes up,” he said.
LEDs are a point source of light with much of the light radiating like a star in all directions.
“When LED fixtures are mounted overhead in an indoor farm much of the light goes to the side obliquely,” Mitchell said. “Not all of the light is going down towards the plants. There is a significant amount of photons wasted falling outside of the cropping area. There’s not much that can be done about it other than to move the lights closer to the plants.”
Because LEDs are cool, unlike high intensity discharge (HID) lamps, the separation distance between LED fixtures and the plants can be decreased without burning the plants.
“The separation distance can be reduced so that most of the obliquely emitted photons actually are captured by the crop surface instead of going off the edge of the bench,” Mitchell said. “Regardless of whether growers run LED fixtures along the bench or across the bench, they don’t want gradients of crop growth. Growers want just as much growth on the edges as in the middle of the bench. This can cause growers to mount lights not only in the middle of the bench, but also out towards the edges. The further toward the edges the fixtures are mounted, the more photons are lost.”
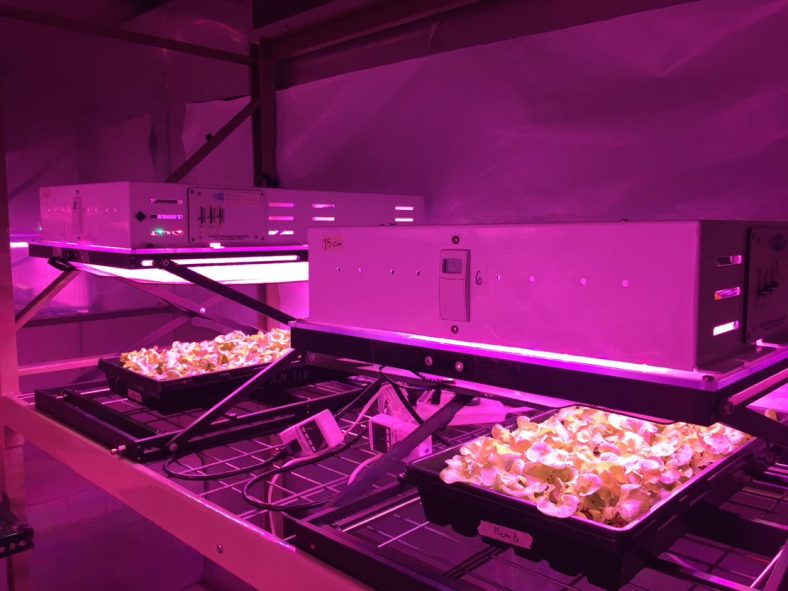
Putting more light on the plants
Sheibani is studying two scenarios of close-canopy lighting. One scenario is as the LED lights are placed closer to the plants, the light is dimmed. Even though the light is dimmed, there is the same intensity of light at the plant surface because more laterally emitted photons are captured, but less electricity is used. In a second scenario, Sheibani placed the LED lights closer to the plants, but did not dim them.
“In this second scenario, placing the fixtures closer to the plants once again reduced the amount of photon loss,” Mitchell said. “In this case, for the same power and energy usage the plant yields increased because the effective light intensity increased. The plants grew faster and bigger. Each increment of closer spacing results in a higher energy utilization efficiency.”
In indoor vertical farms the traditional separation distance between the bottom of the LED fixtures and the top of the crop is 40-50 centimeters.
“We have tested separation distances between the fixtures and plants of 45, 35, 25 and 15 centimeters,” Mitchell said. “We found that energy utilization efficiency increases linearly as the lights are placed closer to the plants. This should be relatively easy to implement in most indoor farms, but may require some design modifications from equipment suppliers.”
Mitchell explained the reason the two scenarios were studied is because some indoor farms are equipped with non-dimmable LED lights.
“In the case of non-dimmable LED fixtures, when the lights are brought closer to the plants, the energy draw by the lights is the same, but the yield goes up, which means the plants grow faster,” he said. “This means the plants can reach the same biomass and be harvested earlier or the harvest date can remain the same and more biomass can be produced. This gives growers the option to use close-canopy lighting for what works best for their production needs.”
Mitchell points out that not every LED fixture commercially available works well in close-canopy lighting applications.
“There are some LED lights where the distribution of colors is not uniform, where there are clusters of blue light,” he said. “This is not a big deal with a 45-centimeter separation distance between the lights and the plants because with the amount of beam spread there is enough distance for the other colors to overlap the blue light. But when the lights are placed within 25 to 15 centimeters of the plant surface, there are clusters of blue light. Blue light inhibits leaf expansion and promotes leaf coloration. The result can be very strange looking crop stands if close-canopy lighting is done with LEDs with uneven light distribution. Fortunately for growers, most of the commercial LED arrays available today for horticultural lighting are quite uniform.”
For more: Murat Kacira, University of Arizona, Controlled Environment Agriculture Center; mkacira@arizona.edu; http://ceac.arizona.edu/. Cary Mitchell, Purdue University, Horticulture & Landscape Architecture; cmitchel@purdue.edu; https://ag.purdue.edu/department/hla/directory.html#/cmitchel.
This article is property of Urban Ag News and was written by David Kuack, a freelance technical writer in Fort Worth, Texas.
2 Comments
At first glance it appears the lighting design is very poor.
First off the fixtures should not be spaced equidistant.
The LED fixtures must extend beyond the edge of the grow area.
And therefore, it would be more efficient if the fixtures ran the length rather than the width.
It may be much more cost effective to use strips of “white” LED lighting, e.g 2700K 90 CRI.
Covering the LEDs with polycarbonate or acrylic lens/covers is very wasteful.
The height above the canopy must be coordinated with the spacing between the strips.
The cost, reliability, and efficiency of the LED power supplies is critical.
Lighting uniformity across the entire canopy is imperative.
Shelving on wheels adds enormously to efficiency.
All of the photos in this article are provided by the University of Arizona.
Universities measure the lights to insure accuracy in data. These photos should not be seen as commercial designs.